Small drives can mean big energy savings on production lines
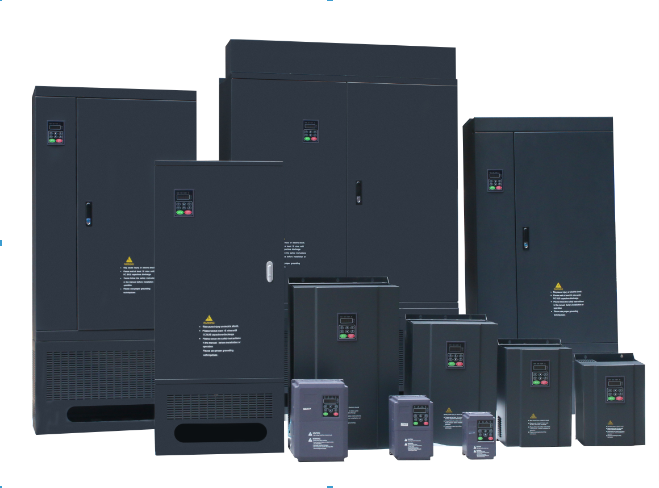
Saving energy on a large scale therefore is not rocket science, one area that is equally as simple, but in many instances is being overlooked is small motors and small drives, often driving continuous process items such as fans, pumps and compressors.
Employing variable speed drives and high efficiency motors to ensure energy efficiency on a new large-scale capital project is not difficult in principle.
Neither is finding the largest HVAC motor on an industrial site and fitting a drive to reduce the overall energy consumption, in order to meet a self-imposed energy saving target.
Equipment efficiency
The high number of smaller motors being used on any one site can often mean that the savings are comparable to that of applying a drive to one large fan motor for example, but the capital investment can be far lower. The contribution to overall equipment efficiency (OEE) is also therefore higher.
"The idea that small drives can make a large contribution to energy saving is borne out by the figures", comments Justin Peters, Technical Manager at AC Tech Lenze and who has played a central role in developing a new simple-to-use Energy Saving Program for customers.
"The recent increases in energy costs have contributed to the faster payoff times for small drives, the overall potential saving is huge and we believe it is currently being overlooked," continues Peters. "The example below is taken directly from the Energy Saving software program that is designed to be used for calculating the savings that can be made in common driven applications with centrifugal loads. This average production line process application is showing an ROI period of just a few months for a 0.75 kW Lenze smd AC drive when compared to a common alternative control method."
There are often just one or two very large motors on a production or processing site, whereas the majority of sites with any level of basic factory process or automation will include many smaller electric motors.
Just a few production lines can include hundreds of small motors and it is in these situations where the cumulative savings could be huge; almost two thirds of industrial electricity consumption is due to the running of electric motors and drive systems, the cost was recently estimated at over £3 billion pa, a large proportion of which is attributable to running fans, pumps and compressors.
he other attractive reasons for focussing on small drives for energy saving are the speed at which they can be installed and their simplicity of use. The latest generation of low-cost Lenze smd AC drives for example are ready-to-run straight from the box with useful factory settings already in the memory chip for fan and pump applications and simple controls on the front of the drive for speed adjustment and basic programming.
The footprint of a 'sub-micro' drive is also so small now that it can often be fitted directly into the existing control panel on a machine and wired in with a minimum off fuss, (the footprint of a 0.25kW Lenze smd drive for example is just 93mm wide by 83mm deep). This ease of use means that the smd drive can be installed and working in a matter of minutes.
Efficiency programme
The result is that by focussing on small drives for energy saving the activity does not have to be a capital or labour intensive one, and can be implemented very quickly. For a modest investment, many smaller motors from 0.25kW up to 22kW could be included in an energy efficiency improvement programme and provide cumulative savings that could reduce energy costs by thousands of pounds.